The Russian lathe accident video has captured global attention, serving as a stark reminder of the dangers associated with industrial machinery. This incident, which occurred in a manufacturing facility, showcases the catastrophic consequences of neglecting safety protocols. The video, widely circulated online, depicts a horrifying moment when a lathe machine malfunctioned, leading to severe injuries. Such accidents not only highlight the risks faced by workers but also emphasize the urgent need for improved safety measures in industrial settings.
Industrial accidents, like the one documented in the Russian lathe accident video, are not isolated incidents but rather a reflection of systemic issues within the manufacturing sector. These incidents often stem from a combination of factors, including inadequate training, outdated equipment, and a lack of stringent safety regulations. The video has sparked discussions among safety experts, policymakers, and the general public, prompting a reevaluation of current safety practices. Understanding the root causes of such accidents is crucial for preventing future occurrences and ensuring the well-being of workers.
Beyond the immediate shock and horror, the Russian lathe accident video serves as an educational tool, shedding light on the importance of vigilance and adherence to safety protocols. It has become a case study for safety training programs, emphasizing the need for continuous improvement in workplace safety. By examining this incident in detail, we can identify gaps in safety measures and implement strategies to mitigate risks. This article delves into the causes, implications, and lessons of the Russian lathe accident video, aiming to contribute to a safer industrial environment worldwide.
Read also:Why Hdhub4u Movie Is Revolutionizing The Streaming Experience
Table of Contents
- What Are the Causes of the Russian Lathe Accident Video?
- How Does the Russian Lathe Accident Video Impact Industrial Safety?
- What Lessons Can We Learn from the Russian Lathe Accident Video?
- What Are the Common Safety Measures to Prevent Lathe Accidents?
- How Can Technology Reduce Risks in Lathe Operations?
- Why Is Worker Training Critical in Preventing Lathe Accidents?
- What Role Do Regulations Play in Lathe Safety?
- Frequently Asked Questions About Lathe Safety
What Are the Causes of the Russian Lathe Accident Video?
The Russian lathe accident video, while shocking, provides a critical opportunity to analyze the factors that contributed to this tragic incident. Understanding these causes is essential for preventing similar accidents in the future. One of the primary causes identified in this case was the lack of proper machine maintenance. Lathe machines, like all industrial equipment, require regular inspections and servicing to ensure they operate safely. In this incident, it was reported that the machine had not undergone routine maintenance, leading to mechanical failures that resulted in the accident.
Another significant factor was the absence of adequate safety training for the workers operating the lathe. Many industrial accidents occur because workers are either unaware of the risks associated with the equipment they are using or do not know how to respond in emergency situations. In the case of the Russian lathe accident video, it was evident that the operator lacked the necessary training to identify potential hazards or take corrective actions. This highlights the importance of comprehensive safety training programs that equip workers with the knowledge and skills to handle machinery safely.
Furthermore, the incident underscores the dangers of complacency in the workplace. Over time, workers may become desensitized to the risks posed by machinery, leading to a disregard for safety protocols. In this case, the operator was reportedly not wearing the required personal protective equipment (PPE), such as gloves and safety goggles, which could have mitigated the severity of the injuries. Additionally, the lack of proper machine guarding—a safety feature designed to protect operators from moving parts—played a crucial role in the accident. These factors, combined with the high-pressure environment of industrial workplaces, create a perfect storm for accidents like the one captured in the Russian lathe accident video.
How Human Error Contributes to Lathe Accidents
Human error is a significant contributing factor in many industrial accidents, including those involving lathes. In the context of the Russian lathe accident video, several instances of human error can be identified. For example, the operator may have been distracted or fatigued, leading to a lapse in judgment. Fatigue, often caused by long working hours or inadequate rest, impairs a worker’s ability to focus and make sound decisions. This is particularly dangerous when operating heavy machinery like lathes, where a momentary lapse can have catastrophic consequences.
Another form of human error is the improper use of machinery. Workers may attempt to bypass safety features or use equipment in ways it was not designed for, increasing the risk of accidents. In the case of the Russian lathe accident video, it was reported that the operator was attempting to adjust the machine while it was still in operation, a clear violation of safety protocols. Such actions are often driven by a desire to save time or increase productivity, but they come at the cost of safety. Addressing human error requires a combination of training, supervision, and a culture of accountability in the workplace.
The Role of Outdated Equipment in Lathe Accidents
Outdated or poorly maintained equipment is another critical factor that contributed to the Russian lathe accident video. Many industrial facilities, particularly in regions with less stringent regulations, continue to use machinery that is decades old. While these machines may still function, they often lack modern safety features and are more prone to mechanical failures. In this incident, the lathe machine in question was reportedly over 20 years old and had not been upgraded to meet current safety standards.
Read also:Kat Timpf Due Date 2025 A Comprehensive Guide
The lack of modern safety features, such as automatic shut-off mechanisms or emergency stop buttons, significantly increases the risk of accidents. Additionally, older machines are more likely to experience wear and tear, which can lead to malfunctions. In the case of the Russian lathe accident video, the machine’s spindle reportedly detached due to a combination of wear and improper maintenance. This highlights the importance of regularly updating and replacing outdated equipment to ensure worker safety.
How Does the Russian Lathe Accident Video Impact Industrial Safety?
The Russian lathe accident video has had a profound impact on industrial safety practices worldwide, serving as a wake-up call for manufacturers, safety regulators, and workers alike. The widespread dissemination of the video has brought industrial safety to the forefront of public discourse, prompting organizations to reevaluate their safety protocols. One of the most immediate impacts has been the increased emphasis on safety audits and inspections. Companies are now more vigilant in identifying potential hazards and ensuring that machinery is maintained to the highest standards.
Additionally, the video has underscored the importance of fostering a culture of safety within industrial workplaces. Many organizations have begun implementing comprehensive safety training programs that not only educate workers about the risks associated with machinery but also empower them to take proactive measures to prevent accidents. This shift in focus from reactive to proactive safety measures is a direct response to the lessons learned from the Russian lathe accident video. By prioritizing safety, companies can reduce the likelihood of accidents and create a safer working environment for their employees.
How Has the Video Influenced Safety Regulations?
The Russian lathe accident video has also played a pivotal role in shaping safety regulations and policies. In response to the incident, several countries have introduced stricter guidelines for the operation of industrial machinery, particularly lathes. These regulations mandate regular inspections, mandatory safety training for operators, and the installation of modern safety features on all machinery. For example, some regions have made it compulsory for companies to install machine guards and automatic shut-off mechanisms on lathes to prevent similar accidents.
Furthermore, the video has prompted regulatory bodies to conduct more frequent audits of industrial facilities to ensure compliance with safety standards. Non-compliance is now met with severe penalties, including fines and temporary shutdowns, to deter negligence. This increased regulatory scrutiny has forced companies to prioritize safety, not only to protect their workers but also to avoid legal and financial repercussions.
What Are the Long-Term Implications for the Manufacturing Industry?
In the long term, the Russian lathe accident video is likely to have a lasting impact on the manufacturing industry. One of the most significant implications is the growing demand for safer and more technologically advanced machinery. Manufacturers are now investing in equipment that incorporates the latest safety innovations, such as sensors and AI-driven monitoring systems, to minimize risks. This shift towards modernization not only enhances safety but also improves efficiency and productivity.
Moreover, the incident has highlighted the need for continuous improvement in safety practices. Companies are now more willing to collaborate with safety experts and invest in research to identify emerging risks and develop effective mitigation strategies. This proactive approach is expected to reduce the incidence of accidents and create a safer and more sustainable manufacturing environment.
What Lessons Can We Learn from the Russian Lathe Accident Video?
The Russian lathe accident video offers a wealth of lessons that can be applied to improve safety practices in industrial settings. One of the most important takeaways is the critical role of regular maintenance in preventing accidents. Machinery that is not properly maintained is more likely to malfunction, posing a significant risk to workers. By implementing a robust maintenance schedule and adhering to it, companies can ensure that their equipment remains in safe working condition.
Another key lesson is the importance of fostering a culture of safety within the workplace. This involves not only providing workers with the necessary training but also encouraging them to speak up when they identify potential hazards. A culture of safety empowers workers to take ownership of their well-being and that of their colleagues, creating a more vigilant and proactive workforce. The Russian lathe accident video serves as a reminder that safety is everyone’s responsibility.
How Can Companies Promote a Safety-First Mindset?
Promoting a safety-first mindset requires a multi-faceted approach that involves leadership, training, and communication. Leaders within an organization must prioritize safety and lead by example, demonstrating their commitment to creating a safe working environment. This can be achieved by allocating resources for safety initiatives, conducting regular safety meetings, and recognizing employees who contribute to improving safety practices.
Training programs should be designed to be engaging and interactive, ensuring that workers not only understand the risks but also know how to mitigate them. Additionally, open lines of communication are essential for fostering a safety-first mindset. Workers should feel comfortable reporting hazards or unsafe practices without fear of retaliation. By creating an environment where safety is prioritized, companies can significantly reduce the risk of accidents.
What Role Does Technology Play in Enhancing Safety?
Technology plays a crucial role in enhancing safety in industrial settings. Modern machinery is often equipped with advanced safety features, such as sensors, automatic shut-off mechanisms, and real-time monitoring systems. These technologies can detect potential hazards and alert operators before an accident occurs. In the context of the Russian lathe accident video, the absence of such features contributed to the severity of the incident.
Moreover, technology can be used to track and analyze safety data, enabling companies to identify trends and implement targeted interventions. For example, data collected from sensors can be used to predict when a machine is likely to fail, allowing for preventive maintenance. By leveraging technology, companies can create a safer and more efficient workplace.
What Are the Common Safety Measures to Prevent Lathe Accidents?
Preventing lathe accidents requires a combination of engineering controls, administrative measures, and personal protective equipment (PPE). One of the most effective safety measures is the installation of machine guards, which protect operators from moving parts and prevent accidental contact with the machine. These guards should be regularly inspected to ensure they are functioning correctly and have not been tampered with.
Another critical safety measure is the implementation of lockout/tagout (LOTO) procedures. LOTO ensures that machinery is properly shut off and not able to be started up again prior to the completion of maintenance or repair work. This procedure is essential for preventing accidental startups, which can result in severe injuries. Additionally, workers should be provided with appropriate PPE, such as gloves, safety goggles, and face shields, to protect them from flying debris and other hazards.
How Can Safety Training Reduce Lathe Accidents?
Safety training is one of the most effective ways to reduce lathe accidents. Training programs should cover the proper operation of machinery, the identification of potential hazards, and the correct use of safety equipment. Workers should also be trained on emergency procedures, such as how to shut off the machine in case of a malfunction. By equipping workers with the necessary knowledge and skills, companies can significantly reduce the risk of accidents.
What Are the Best Practices for Lathe Maintenance?
Regular maintenance is essential
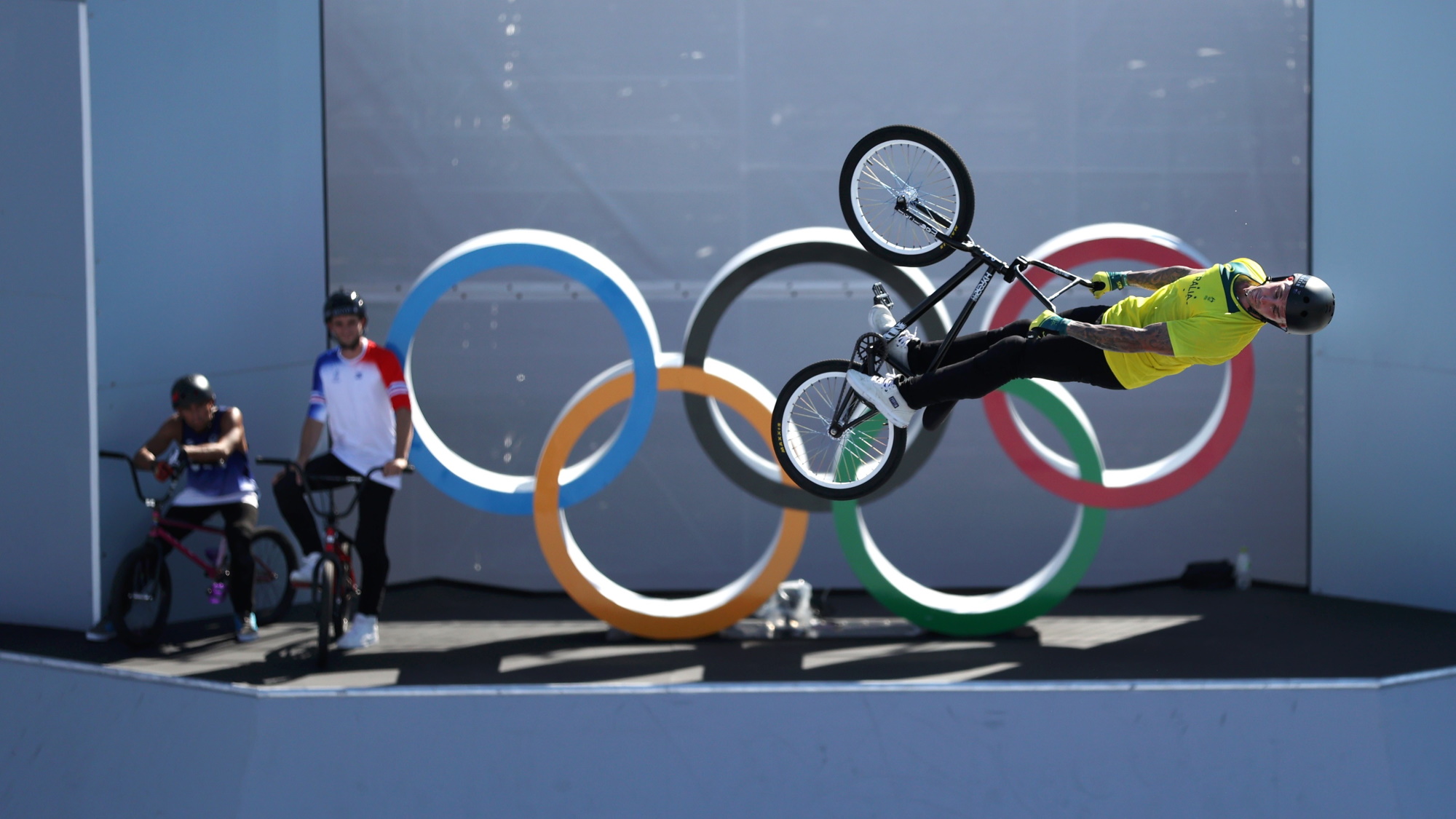
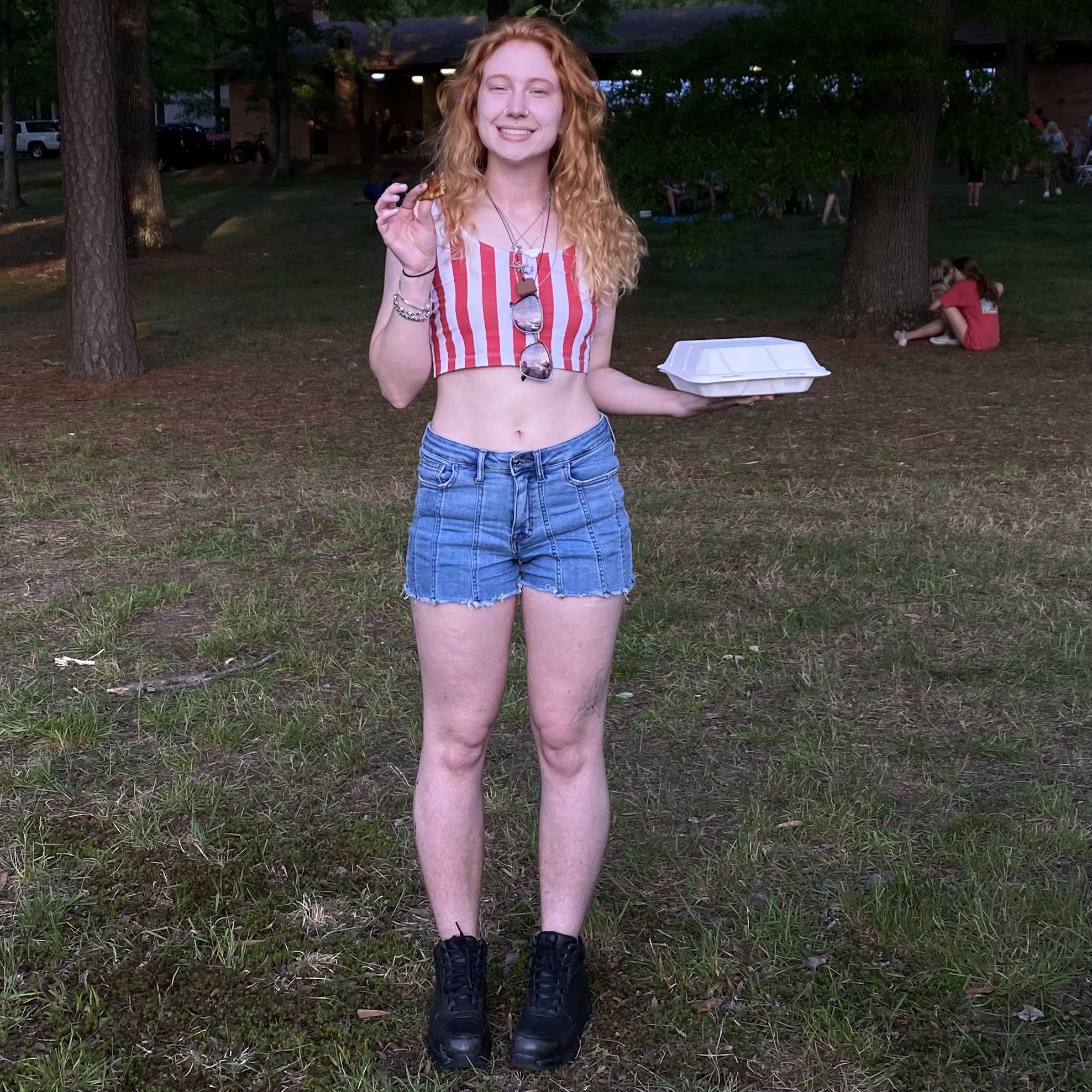