The term "Russian lathe accident video" has gained significant attention in recent years, particularly due to the alarming footage of industrial accidents involving lathes. These videos often depict dangerous incidents that highlight the risks associated with improper use of machinery. Lathes are powerful tools used in manufacturing and metalworking, but when safety protocols are ignored, they can lead to devastating consequences. Understanding these risks is crucial for anyone working in industrial settings or even those curious about workplace safety.
Industrial accidents involving lathes are not limited to Russia; they occur worldwide. However, the viral nature of these videos has brought attention to the importance of safety training and adherence to guidelines. Many of these videos serve as cautionary tales, emphasizing the need for vigilance and proper handling of machinery. In this article, we will explore the causes of lathe accidents, safety measures, and the broader implications of such incidents.
Our goal is to provide a comprehensive guide that not only educates readers about the risks associated with lathes but also offers actionable steps to prevent accidents. Whether you are a professional machinist, a safety officer, or simply someone interested in industrial safety, this article will equip you with valuable insights and practical advice. Let’s dive into the details to better understand the issue and how to address it effectively.
Read also:Kensley Pope The Intriguing Story Behind The Viral Sensation
Table of Contents
- Introduction to Lathe Machines
- Common Causes of Lathe Accidents
- Safety Measures for Lathe Operators
- Case Studies of Lathe Accidents
- The Role of Training and Education
- Legal and Regulatory Standards
- Psychological Impact of Industrial Accidents
- Technological Advancements in Lathe Safety
- How to Respond to a Lathe Accident
- Conclusion and Call to Action
Introduction to Lathe Machines
Lathe machines are essential tools in the manufacturing and metalworking industries. These devices are used to shape materials such as metal, wood, and plastic by rotating the workpiece against a cutting tool. The versatility of lathes makes them indispensable in creating components for various industries, including automotive, aerospace, and construction.
Despite their utility, lathes can be dangerous if not handled properly. The high-speed rotation of the workpiece and the sharp cutting tools pose significant risks to operators. Understanding the mechanics of a lathe machine is the first step in ensuring safe operation. A typical lathe consists of a bed, headstock, tailstock, and carriage, each serving a specific function in the machining process.
Key Components of a Lathe Machine
- Bed: The base of the lathe that provides stability.
- Headstock: Houses the motor and spindle that rotate the workpiece.
- Tailstock: Supports the other end of the workpiece.
- Carriage: Holds the cutting tool and allows it to move along the workpiece.
Common Causes of Lathe Accidents
Lathe accidents often result from a combination of human error, lack of training, and inadequate safety measures. Understanding these causes is critical to preventing future incidents. Below are some of the most common factors contributing to lathe accidents:
1. Improper Use of Personal Protective Equipment (PPE)
One of the primary causes of lathe accidents is the failure to wear appropriate PPE. Operators who neglect to wear safety goggles, gloves, or protective clothing are at a higher risk of injury. Flying debris, sharp edges, and entanglement are common hazards that can be mitigated with proper protective gear.
2. Inadequate Training
Many lathe accidents occur because operators lack the necessary training to use the equipment safely. Training should cover not only the technical aspects of operating a lathe but also emergency procedures and safety protocols.
3. Machine Malfunctions
Old or poorly maintained machines are more likely to malfunction, leading to accidents. Regular maintenance and inspections are essential to ensure that lathes are functioning correctly and safely.
Read also:Exploring Lara Trumps Faith Is Lara Trump Catholic
Safety Measures for Lathe Operators
Ensuring the safety of lathe operators requires a combination of proper training, adherence to safety protocols, and the use of advanced safety features. Below are some critical safety measures that can help prevent lathe accidents:
1. Wear Proper Personal Protective Equipment (PPE)
- Always wear safety goggles to protect your eyes from flying debris.
- Use gloves to protect your hands from sharp edges and hot materials.
- Wear fitted clothing to avoid entanglement in the machine.
2. Conduct Regular Maintenance
Regular maintenance of lathe machines is crucial to prevent malfunctions. This includes checking for loose parts, lubricating moving components, and ensuring that safety guards are in place.
3. Implement Safety Protocols
Establish clear safety protocols for operating lathes, including lockout/tagout procedures to prevent accidental startups. Operators should also be trained to recognize potential hazards and respond appropriately.
Case Studies of Lathe Accidents
To better understand the impact of lathe accidents, let’s examine a few real-world case studies. These examples highlight the consequences of negligence and the importance of safety measures.
Case Study 1: The Russian Lathe Accident Video
One of the most widely shared videos involves a lathe accident in a Russian factory. The footage shows an operator losing control of the machine, resulting in severe injuries. This incident underscores the dangers of improper training and lack of safety protocols.
Case Study 2: A U.S. Manufacturing Plant Incident
In another case, a U.S.-based manufacturing plant experienced a lathe accident due to a machine malfunction. The operator was not wearing proper PPE, which exacerbated the severity of the injuries. This case highlights the importance of regular maintenance and adherence to safety guidelines.
The Role of Training and Education
Training and education play a pivotal role in preventing lathe accidents. Operators must be well-versed in the safe operation of machinery and understand the potential risks involved. Below are some key elements of effective training programs:
1. Hands-On Training
Practical, hands-on training allows operators to gain experience in a controlled environment. This type of training helps them develop the skills needed to operate lathes safely.
2. Safety Workshops
Regular safety workshops can reinforce the importance of adhering to safety protocols. These workshops should include demonstrations of proper PPE usage and emergency procedures.
Legal and Regulatory Standards
Various legal and regulatory standards govern the safe operation of industrial machinery, including lathes. Compliance with these standards is essential to ensure the safety of workers and avoid legal repercussions.
OSHA Regulations
In the United States, the Occupational Safety and Health Administration (OSHA) sets guidelines for workplace safety. These regulations include requirements for machine guarding, PPE, and training programs.
International Standards
Internationally, organizations such as the International Organization for Standardization (ISO) provide standards for industrial machinery safety. Adhering to these standards can help prevent accidents and promote a culture of safety.
Psychological Impact of Industrial Accidents
Industrial accidents, including those involving lathes, can have a profound psychological impact on workers. The trauma of experiencing or witnessing an accident can lead to anxiety, depression, and post-traumatic stress disorder (PTSD).
Support Systems for Workers
Employers should provide access to counseling and mental health resources for workers affected by industrial accidents. Creating a supportive work environment can help employees cope with the psychological effects of such incidents.
Technological Advancements in Lathe Safety
Recent advancements in technology have led to the development of safer lathe machines. Features such as automatic shut-off systems, improved machine guards, and smart sensors can significantly reduce the risk of accidents.
Smart Sensors and Automation
Smart sensors can detect abnormalities in machine operation and trigger automatic shut-offs to prevent accidents. Automation technologies also reduce the need for manual intervention, minimizing human error.
How to Respond to a Lathe Accident
In the event of a lathe accident, it is crucial to respond quickly and effectively. Below are the steps to take in such a situation:
1. Secure the Area
Ensure that the machine is turned off and the area is safe before attempting to assist the injured person.
2. Provide First Aid
Administer first aid if you are trained to do so. Call emergency services immediately for severe injuries.
3. Report the Incident
Document the incident and report it to the appropriate authorities. This information can be used to prevent future accidents.
Conclusion and Call to Action
In conclusion, lathe accidents are a serious concern in industrial settings, and understanding their causes and prevention methods is crucial for ensuring workplace safety. By adhering to safety protocols, undergoing proper training, and utilizing technological advancements, we can significantly reduce the risk of accidents.
We encourage readers to share this article with colleagues and friends who may benefit from this information. Additionally, feel free to leave a comment below with your thoughts or experiences related to industrial safety. Together, we can create a safer working environment for everyone.
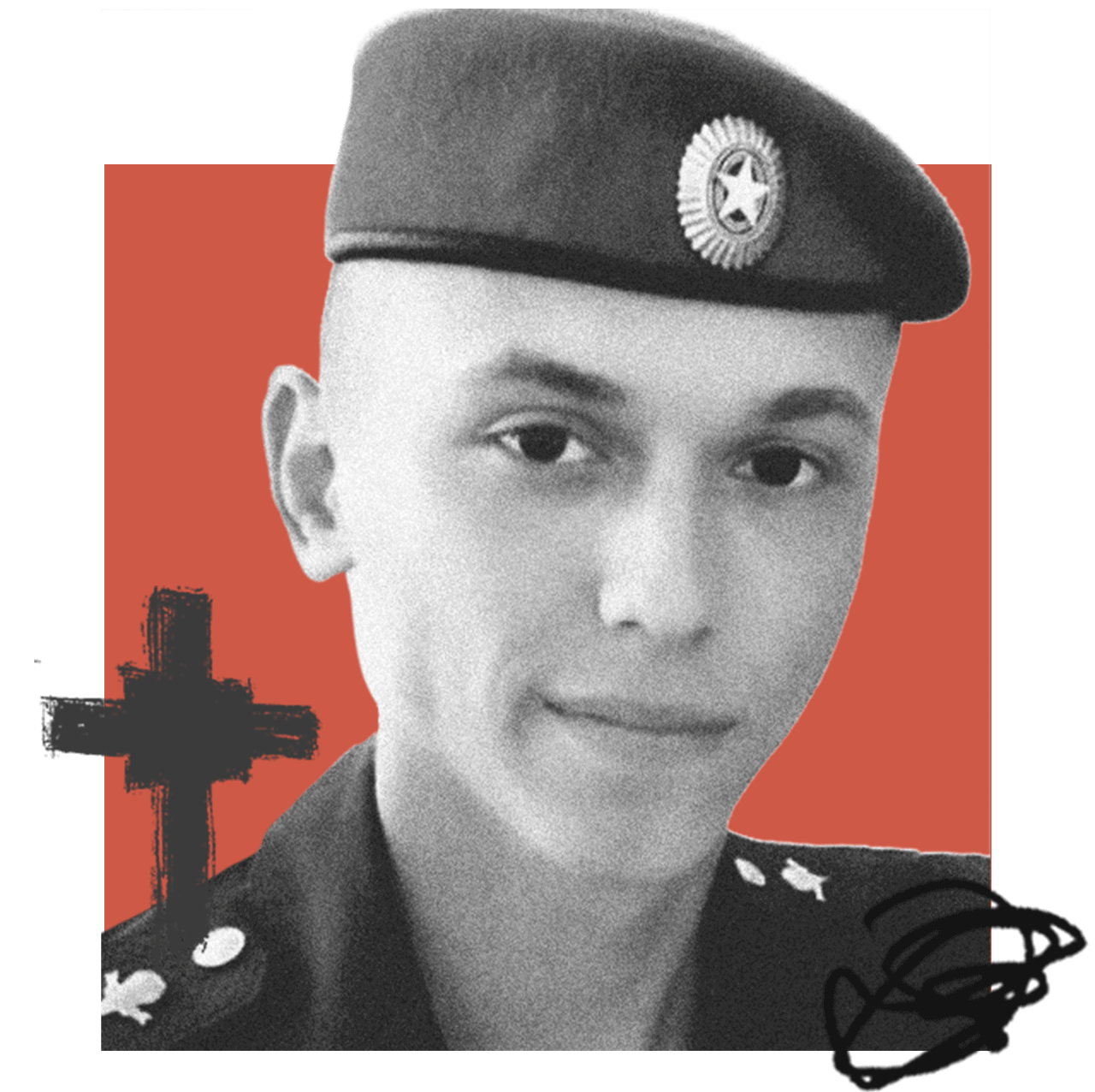
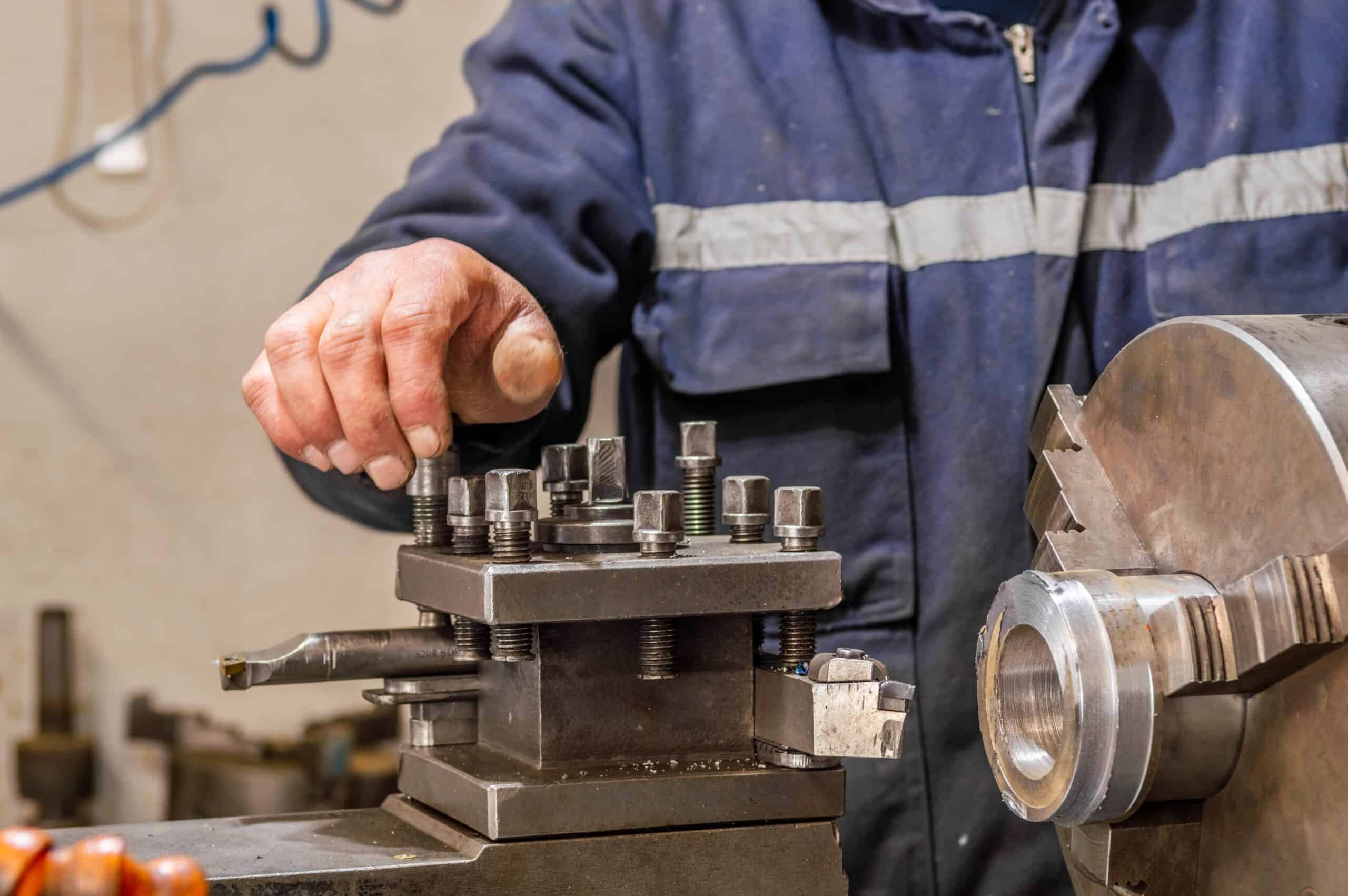