Are you curious about RUL and how it can impact your life or business? RUL, or Remaining Useful Life, is a critical concept in various industries, especially in predictive maintenance, engineering, and asset management. Understanding RUL allows organizations to optimize their operations, reduce costs, and enhance safety. In this article, we will delve deep into the concept of RUL, its applications, and how you can leverage it to improve efficiency. Whether you're a professional in the field or just someone looking to expand your knowledge, this guide is tailored to provide you with valuable insights.
Predictive maintenance has become a cornerstone of modern industrial operations. One of the key metrics used in this domain is RUL, which helps in determining when a piece of equipment is likely to fail. By predicting failure points, businesses can schedule maintenance activities more effectively, minimizing downtime and maximizing productivity. This article will explore the intricacies of RUL, its calculation methods, and its real-world applications.
As we proceed, you'll discover how RUL is not just a technical term but a transformative approach that can revolutionize the way industries operate. From manufacturing to aviation, RUL is reshaping how assets are managed. By the end of this article, you'll have a comprehensive understanding of RUL and how to implement it in your professional or personal projects.
Read also:Pierre Poilievre Height A Comprehensive Look At The Rising Political Star
Table of Contents
What is RUL?
RUL, or Remaining Useful Life, refers to the estimated time left before a machine, component, or system is expected to fail. It is a predictive metric used to assess the condition of an asset and determine when maintenance or replacement is necessary. RUL is particularly important in industries where equipment failure can lead to significant financial losses or safety risks.
The concept of RUL is rooted in predictive maintenance, a strategy that uses data analysis and machine learning to predict when equipment will require maintenance. By understanding the RUL of an asset, organizations can proactively address potential issues, reducing the likelihood of unexpected breakdowns.
Why is RUL Important?
RUL is crucial for several reasons:
- Cost Efficiency: Predictive maintenance based on RUL can reduce maintenance costs by avoiding unnecessary repairs and minimizing downtime.
- Safety: By predicting failures, organizations can prevent accidents and ensure the safety of their workforce.
- Operational Efficiency: Understanding RUL allows businesses to optimize their operations by scheduling maintenance at the most opportune times.
The Importance of RUL in Modern Industries
In today's fast-paced industrial environment, the ability to predict equipment failure is a game-changer. RUL plays a pivotal role in industries such as manufacturing, aviation, healthcare, and energy. By leveraging RUL, organizations can transition from reactive to proactive maintenance strategies, leading to significant improvements in efficiency and reliability.
For example, in the aviation industry, RUL is used to monitor the health of aircraft engines. By predicting when an engine component is likely to fail, airlines can schedule maintenance during non-peak hours, reducing the risk of delays and cancellations. Similarly, in the manufacturing sector, RUL helps in optimizing production schedules and reducing waste.
Industries That Benefit from RUL
- Manufacturing: Predictive maintenance using RUL minimizes downtime and increases production efficiency.
- Aviation: Ensures safety and reliability by predicting engine and component failures.
- Healthcare: Monitors medical equipment to prevent malfunctions during critical procedures.
- Energy: Optimizes the performance of power plants and renewable energy systems.
Methods of Calculating RUL
Calculating RUL involves a combination of data collection, analysis, and modeling. There are several methods used to estimate RUL, each with its own advantages and limitations. Below, we explore some of the most common techniques:
Read also:Filippo Testa Balmain Net Worth A Deep Dive Into The World Of Fashion And Wealth
Data-Driven Approaches
Data-driven methods rely on historical data and machine learning algorithms to predict RUL. These approaches are particularly effective when large datasets are available. Common techniques include:
- Regression Analysis: Uses statistical models to predict future trends based on historical data.
- Machine Learning: Algorithms such as neural networks and decision trees are used to identify patterns and predict failures.
- Time Series Analysis: Analyzes data points collected over time to forecast future behavior.
Physics-Based Models
Physics-based models use the principles of physics and engineering to estimate RUL. These models are often more accurate but require detailed knowledge of the system being analyzed. Examples include:
- Finite Element Analysis (FEA): Simulates the behavior of components under various conditions.
- Stress-Strain Analysis: Evaluates the mechanical properties of materials to predict failure points.
Applications of RUL Across Industries
RUL is not limited to a single industry; its applications are vast and varied. Below, we explore how different sectors utilize RUL to enhance their operations:
Manufacturing
In manufacturing, RUL is used to monitor the health of machinery and equipment. By predicting when a machine is likely to fail, manufacturers can schedule maintenance during off-peak hours, reducing downtime and increasing productivity. Additionally, RUL helps in optimizing spare parts inventory, ensuring that critical components are available when needed.
Aviation
The aviation industry relies heavily on RUL to ensure the safety and reliability of aircraft. By monitoring the RUL of engines and other critical components, airlines can prevent catastrophic failures and ensure passenger safety. RUL also helps in optimizing maintenance schedules, reducing costs, and improving operational efficiency.
Healthcare
In healthcare, RUL is used to monitor medical equipment such as MRI machines and ventilators. By predicting when a device is likely to fail, hospitals can prevent malfunctions during critical procedures, ensuring patient safety. RUL also helps in optimizing the maintenance of medical equipment, reducing downtime and improving the quality of care.
Tools and Technologies for RUL Analysis
Several tools and technologies are available to assist in RUL analysis. These tools leverage advanced algorithms and data analytics to provide accurate predictions. Below, we explore some of the most popular tools:
Predictive Maintenance Software
Predictive maintenance software uses machine learning and data analytics to predict RUL. These tools collect data from sensors and other sources, analyze it, and provide insights into the health of equipment. Examples include:
- IBM Maximo: A comprehensive asset management platform that includes predictive maintenance capabilities.
- SAP Predictive Maintenance: Integrates with SAP's enterprise resource planning (ERP) system to provide real-time insights into asset health.
IoT and Sensor Technology
The Internet of Things (IoT) and sensor technology play a crucial role in RUL analysis. Sensors collect data on various parameters such as temperature, vibration, and pressure, which are then analyzed to predict RUL. IoT platforms such as Microsoft Azure and AWS IoT provide the infrastructure needed to process and analyze this data.
Challenges in Implementing RUL
While RUL offers numerous benefits, implementing it can be challenging. Below, we explore some of the common obstacles organizations face when adopting RUL:
Data Quality and Availability
Accurate RUL predictions depend on high-quality data. However, many organizations struggle with data collection and management. Issues such as incomplete datasets, inconsistent data formats, and data silos can hinder RUL analysis.
Technical Expertise
Implementing RUL requires specialized knowledge in data analytics, machine learning, and engineering. Organizations often face a shortage of skilled professionals who can develop and maintain RUL systems.
Cost and Resource Constraints
Developing and deploying RUL systems can be expensive. Organizations need to invest in hardware, software, and personnel, which can be a significant financial burden, especially for small and medium-sized enterprises.
Case Studies: Success Stories of RUL Implementation
To better understand the impact of RUL, let's explore some real-world case studies:
Case Study 1: Predictive Maintenance in Manufacturing
A leading manufacturing company implemented RUL-based predictive maintenance to monitor the health of its production equipment. By analyzing data from sensors installed on machines, the company was able to predict failures and schedule maintenance proactively. As a result, downtime was reduced by 30%, and maintenance costs decreased by 20%.
Case Study 2: RUL in Aviation
An international airline used RUL to monitor the health of its aircraft engines. By predicting when engine components were likely to fail, the airline was able to schedule maintenance during non-peak hours, reducing delays and cancellations. The implementation of RUL resulted in a 15% increase in operational efficiency and a significant improvement in passenger safety.
Future Trends in RUL
The field of RUL is constantly evolving, with new technologies and methodologies emerging regularly. Below, we explore some of the future trends in RUL:
Integration with AI and Machine Learning
Artificial intelligence (AI) and machine learning are expected to play an increasingly important role in RUL analysis. These technologies can process vast amounts of data and identify patterns that would be difficult for humans to detect, leading to more accurate predictions.
Advancements in IoT
As IoT technology continues to advance, the quality and quantity of data available for RUL analysis will increase. This will enable more precise predictions and better decision-making.
How to Get Started with RUL
If you're interested in implementing RUL in your organization, here are some steps to get started:
Step 1: Assess Your Needs
Identify the assets and equipment that would benefit most from RUL analysis. Consider factors such as criticality, cost of failure, and maintenance frequency.
Step 2: Invest in Technology
Choose the right tools and technologies for RUL analysis. Consider factors such as ease of use, scalability, and integration with existing systems.
Step 3: Train Your Team
Ensure that your team has the necessary skills and knowledge to implement and maintain RUL systems. Provide training in data analytics, machine learning, and predictive maintenance.
Conclusion
RUL is a powerful concept that can transform the way organizations manage their assets. By predicting when equipment is likely to fail, businesses can reduce costs, improve safety, and enhance operational efficiency. Whether you're in manufacturing, aviation, healthcare, or any other industry, understanding and implementing RUL can provide significant benefits.
We hope this article has provided you with a comprehensive understanding of RUL and its applications. If you found this guide helpful, please consider sharing it with your network or leaving a comment below. For more insights and resources, explore our other articles on predictive maintenance and asset management.
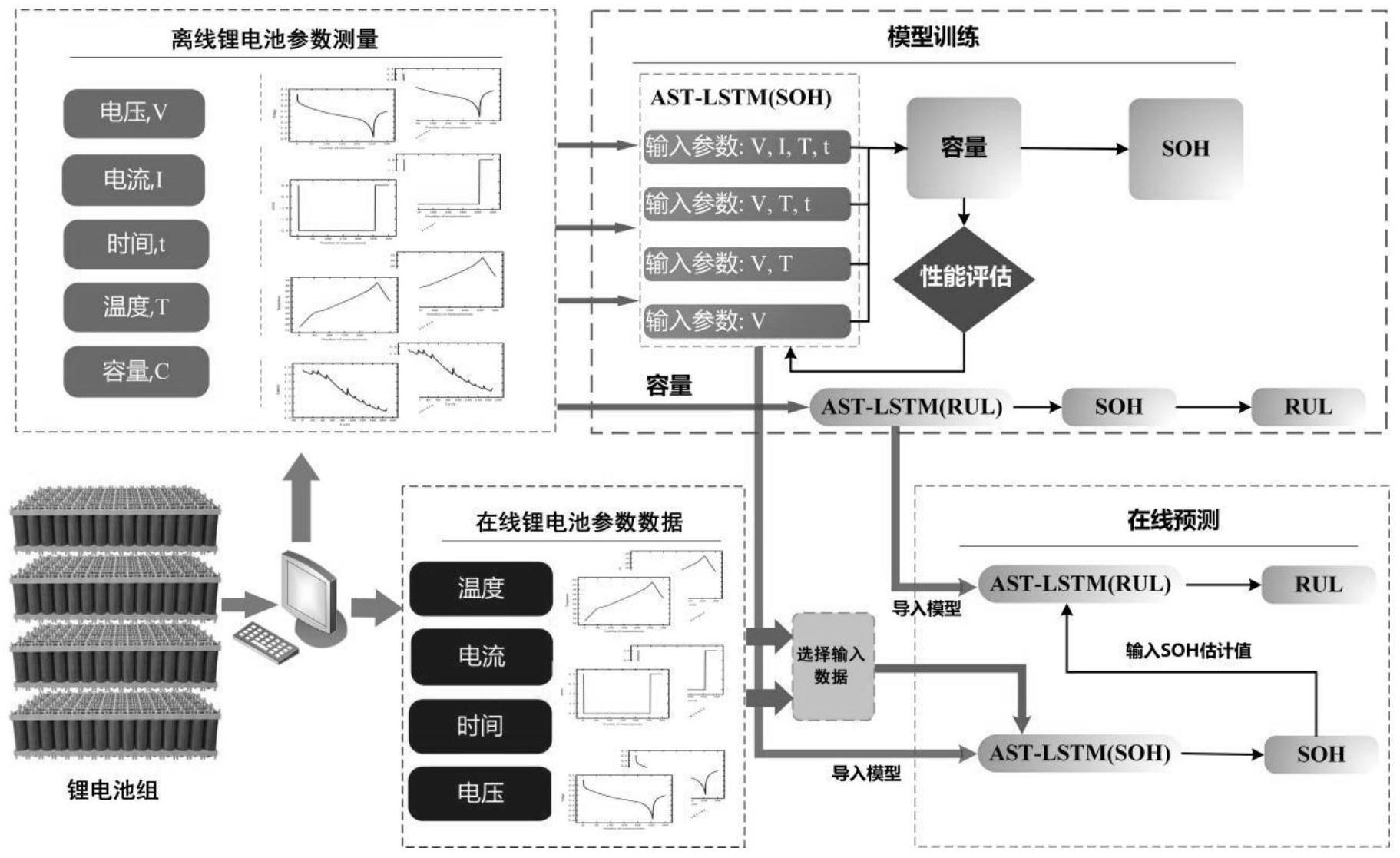
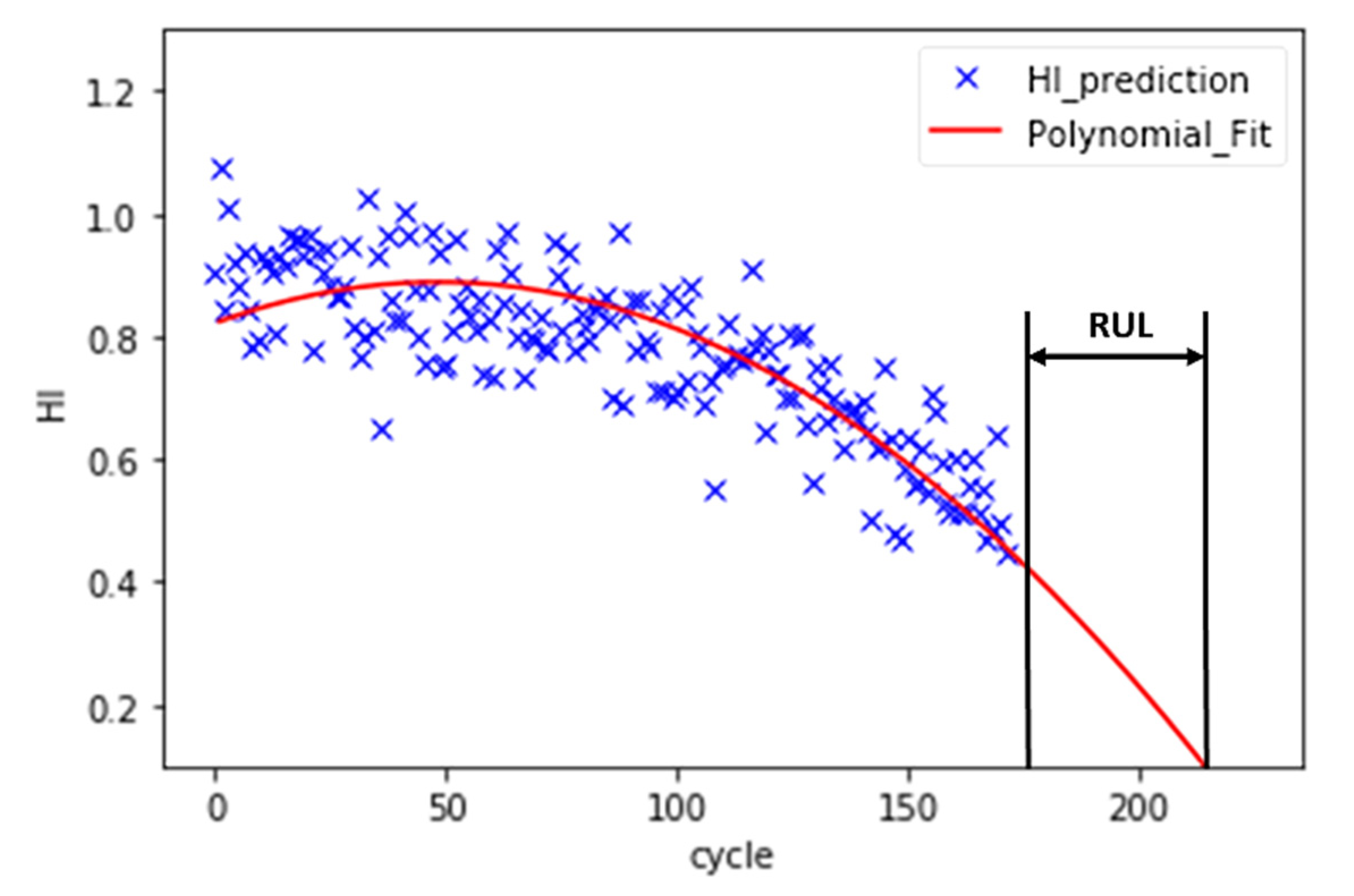