Warehouse floor marking near me is a search term that has gained significant traction among business owners, warehouse managers, and logistics professionals. Whether you're running a small storage facility or managing a large-scale distribution center, proper floor marking is essential for maintaining safety, improving efficiency, and ensuring compliance with industry standards. Floor markings act as visual cues that guide employees, organize inventory, and delineate specific zones within the warehouse. In this article, we will explore everything you need to know about warehouse floor marking, including its benefits, types, implementation strategies, and how to find the best services near you.
Floor marking is not just about painting lines on the floor. It involves a strategic approach to designing a layout that maximizes space utilization, minimizes accidents, and enhances workflow. Many businesses overlook the importance of floor marking until they face challenges such as disorganized inventory, inefficient traffic flow, or safety violations. By understanding the role of floor marking and investing in professional services, you can transform your warehouse into a well-organized and productive environment.
In the following sections, we will delve deeper into the concept of warehouse floor marking, its applications, and how to choose the right materials and service providers. We will also provide actionable tips and insights to help you implement an effective floor marking system tailored to your specific needs. Whether you're looking to improve safety, streamline operations, or comply with regulations, this guide will equip you with the knowledge and tools to achieve your goals.
Read also:Charlie Hunnam And Morgana Mcnelis Split A Comprehensive Look At Their Relationship
Table of Contents
- What is Warehouse Floor Marking?
- Benefits of Warehouse Floor Marking
- Types of Floor Marking Materials
- Choosing the Right Floor Marking Service Near Me
- Designing an Effective Floor Marking Layout
- Compliance and Safety Standards
- Maintenance Tips for Floor Markings
- Common Mistakes to Avoid
- Case Studies and Success Stories
- Conclusion
What is Warehouse Floor Marking?
Warehouse floor marking refers to the process of applying visual indicators, such as lines, symbols, and colors, on the floor to designate specific areas, pathways, and zones within a warehouse. These markings serve as a communication tool for employees, helping them navigate the space efficiently and safely. Floor marking systems are widely used in industries such as manufacturing, logistics, retail, and e-commerce to improve organization and productivity.
Key Components of Floor Marking
- Lines: Used to define boundaries, aisles, and pathways.
- Symbols: Indicate specific actions, such as stop signs, pedestrian crossings, or hazard warnings.
- Colors: Different colors are used to represent various zones, such as red for hazardous areas and yellow for caution zones.
By implementing a well-designed floor marking system, businesses can create a safer and more organized work environment. This not only enhances operational efficiency but also reduces the risk of accidents and injuries.
Benefits of Warehouse Floor Marking
Investing in warehouse floor marking offers numerous advantages that go beyond aesthetics. Below are some of the key benefits:
1. Improved Safety
One of the primary purposes of floor marking is to enhance safety within the warehouse. By clearly defining pedestrian walkways, forklift lanes, and hazardous areas, businesses can minimize the risk of accidents. For example, using contrasting colors for pedestrian and vehicle zones ensures that employees and equipment operators are aware of their surroundings.
2. Enhanced Efficiency
Floor markings help streamline operations by organizing inventory and equipment. Clearly marked storage areas and aisles make it easier for employees to locate items, reducing the time spent searching for products. This leads to faster order fulfillment and improved productivity.
3. Compliance with Regulations
Many industries are subject to strict safety and operational regulations. Proper floor marking ensures compliance with standards set by organizations such as OSHA (Occupational Safety and Health Administration). Non-compliance can result in fines, legal issues, and reputational damage.
Read also:Unveiling The Truth About 9xmoviesin Is It Safe And Legal
4. Cost-Effective Solution
Compared to other warehouse optimization strategies, floor marking is a cost-effective solution. The materials and installation costs are relatively low, and the long-term benefits outweigh the initial investment.
Types of Floor Marking Materials
When it comes to warehouse floor marking, choosing the right materials is crucial for durability and effectiveness. Below are some of the most commonly used materials:
1. Paint
Traditional floor paint is an affordable option for marking warehouse floors. However, it may not be as durable as other materials and requires regular maintenance. Paint is best suited for low-traffic areas.
2. Tape
Floor marking tape is a popular choice due to its ease of installation and versatility. It comes in various colors, patterns, and materials, such as vinyl and polyester. Tape is ideal for temporary or semi-permanent markings.
3. Epoxy Coatings
Epoxy coatings provide a durable and long-lasting solution for high-traffic areas. They are resistant to chemicals, abrasions, and heavy loads, making them suitable for industrial environments.
4. Stencils
Stencils are used in conjunction with paint or tape to create consistent and professional-looking markings. They are particularly useful for applying symbols and logos.
Choosing the Right Floor Marking Service Near Me
Finding the right floor marking service provider is essential to ensure quality results. Here are some factors to consider when selecting a service:
1. Experience and Expertise
Look for a company with a proven track record in warehouse floor marking. Experienced providers will have the knowledge and skills to design and implement an effective system tailored to your needs.
2. Portfolio and References
Review the provider's portfolio and ask for references from past clients. This will give you an idea of their capabilities and the quality of their work.
3. Material Options
Ensure that the service provider offers a wide range of materials to choose from. This allows you to select the best option for your specific requirements and budget.
4. Customer Support
A reliable provider should offer excellent customer support, from the initial consultation to post-installation maintenance. This ensures a smooth and hassle-free experience.
Designing an Effective Floor Marking Layout
Creating an effective floor marking layout requires careful planning and consideration. Below are some steps to guide you through the process:
1. Assess Your Needs
Start by evaluating your warehouse's specific needs. Identify areas that require markings, such as storage zones, loading docks, and pedestrian pathways.
2. Choose the Right Colors
Use standardized color codes to represent different zones and functions. For example, yellow is commonly used for caution zones, while red indicates hazardous areas.
3. Optimize Traffic Flow
Design the layout to minimize congestion and ensure smooth traffic flow. Clearly marked aisles and pathways will help prevent bottlenecks and improve efficiency.
4. Incorporate Symbols and Signs
In addition to lines and colors, use symbols and signs to convey specific instructions or warnings. This enhances communication and reduces the risk of misunderstandings.
Compliance and Safety Standards
Warehouse floor marking must adhere to industry-specific regulations and safety standards. Below are some key guidelines to keep in mind:
OSHA Standards
OSHA provides detailed guidelines for floor marking in industrial environments. For example, aisle markings must be at least 2 inches wide, and color codes should be consistent throughout the facility.
ANSI Standards
The American National Standards Institute (ANSI) offers additional recommendations for floor marking, including the use of standardized symbols and colors.
Local Regulations
Be sure to check local regulations and building codes to ensure compliance. Some regions may have specific requirements for floor marking materials and designs.
Maintenance Tips for Floor Markings
Regular maintenance is essential to ensure the longevity and effectiveness of floor markings. Here are some tips to keep your markings in top condition:
1. Clean Regularly
Dirt, dust, and spills can obscure floor markings and reduce their visibility. Clean the marked areas regularly using appropriate cleaning agents.
2. Inspect for Damage
Conduct routine inspections to identify any signs of wear and tear. Replace damaged markings promptly to maintain safety and compliance.
3. Use Durable Materials
Invest in high-quality materials that can withstand heavy traffic and harsh conditions. This will minimize the need for frequent replacements.
Common Mistakes to Avoid
While implementing floor marking, it's important to avoid common pitfalls that can compromise its effectiveness. Below are some mistakes to watch out for:
1. Poor Planning
Failing to plan the layout properly can lead to disorganized markings and inefficient use of space. Take the time to assess your needs and design a comprehensive system.
2. Inconsistent Color Codes
Using inconsistent or non-standardized color codes can create confusion among employees. Stick to industry-standard colors to ensure clarity.
3. Neglecting Maintenance
Ignoring maintenance can result in faded or damaged markings, which can pose safety risks. Make maintenance a priority to keep your system in optimal condition.
Case Studies and Success Stories
Many businesses have successfully implemented warehouse floor marking systems to achieve significant improvements. Below are a few examples:
Case Study 1: Retail Distribution Center
A large retail chain implemented a comprehensive floor marking system in its distribution center. By clearly defining storage zones and optimizing traffic flow, the company reduced order processing time by 20% and improved employee safety.
Case Study 2: Manufacturing Facility
A manufacturing facility used epoxy coatings for its floor markings, resulting in a durable and long-lasting solution. The company reported a 30% reduction in accidents and improved compliance with safety regulations.
Conclusion
Warehouse floor marking near me is more than just a search term; it represents a critical investment in safety, efficiency, and compliance. By implementing a well-designed floor marking system, businesses can create a safer and more organized work environment, streamline operations, and meet regulatory requirements. Whether you're looking to improve traffic flow, organize inventory, or enhance safety, professional floor marking services can help you achieve your goals.
Take the first step today by assessing your warehouse's needs and consulting with a trusted floor marking service provider. Share your thoughts in the comments below, or explore our other articles for more tips on warehouse optimization. Together, let's create a safer and more productive workspace!
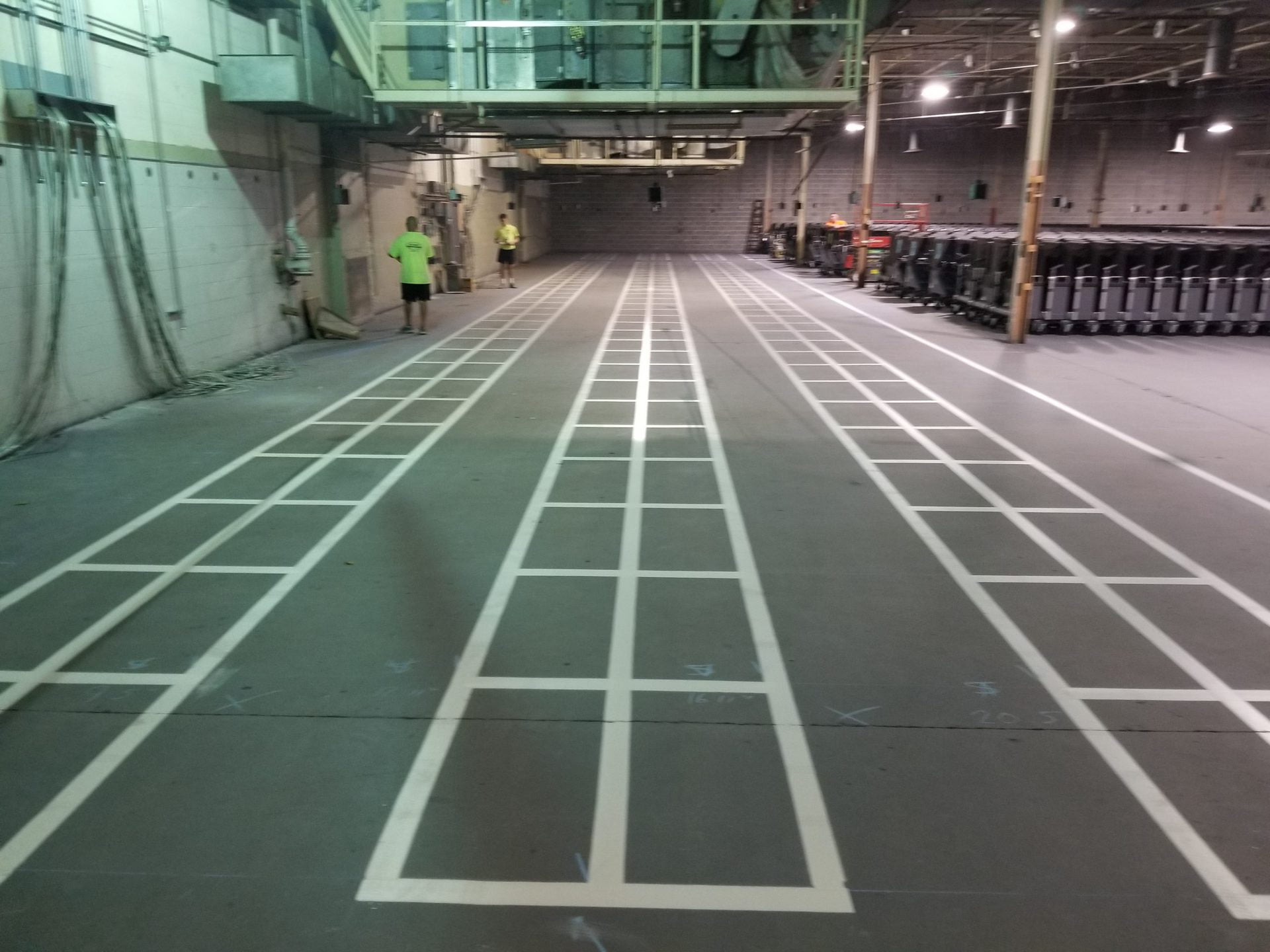
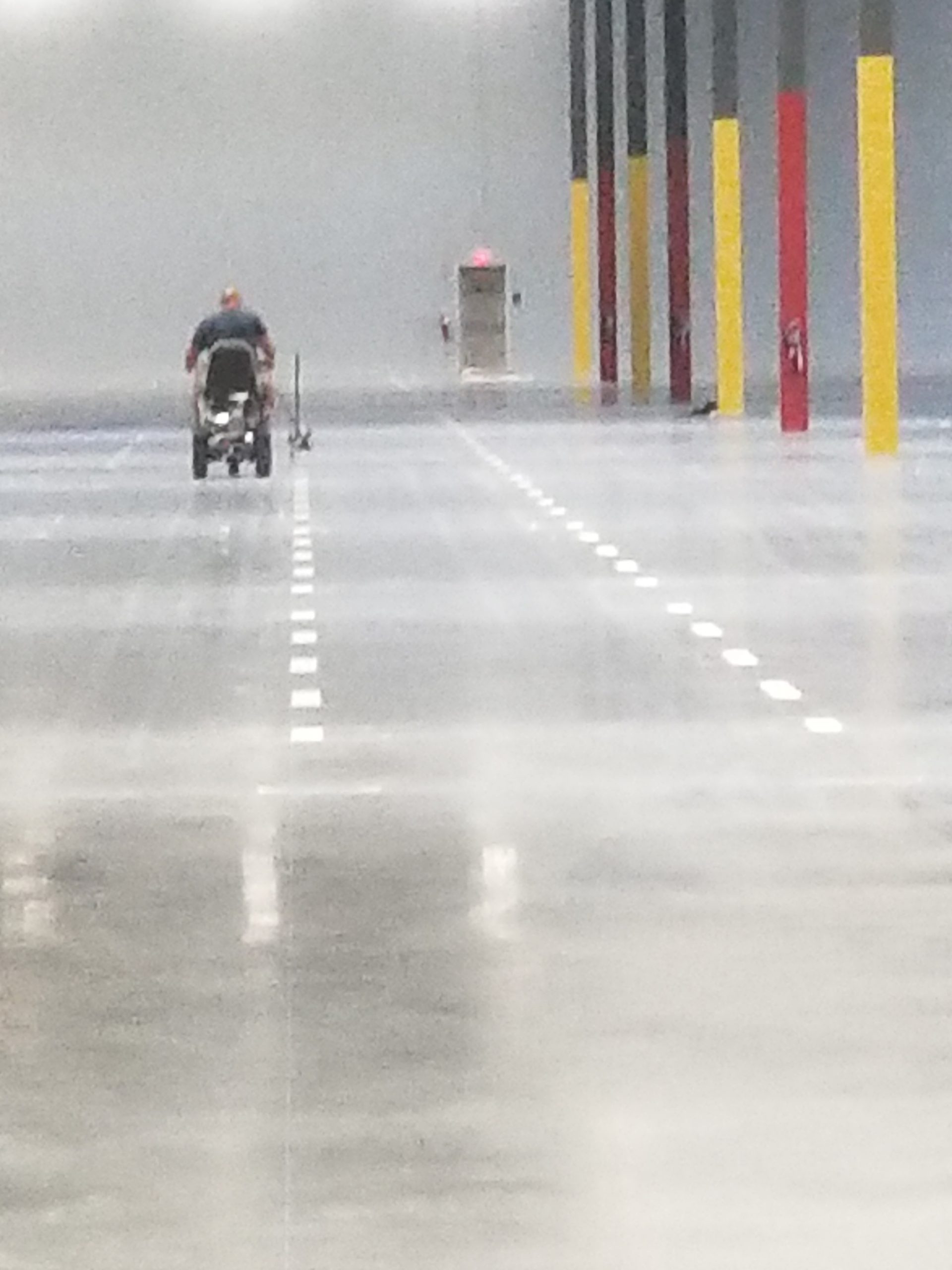